Expert Walk In Freezer Repair Services: Quick Solutions for Your Refrigeration Needs
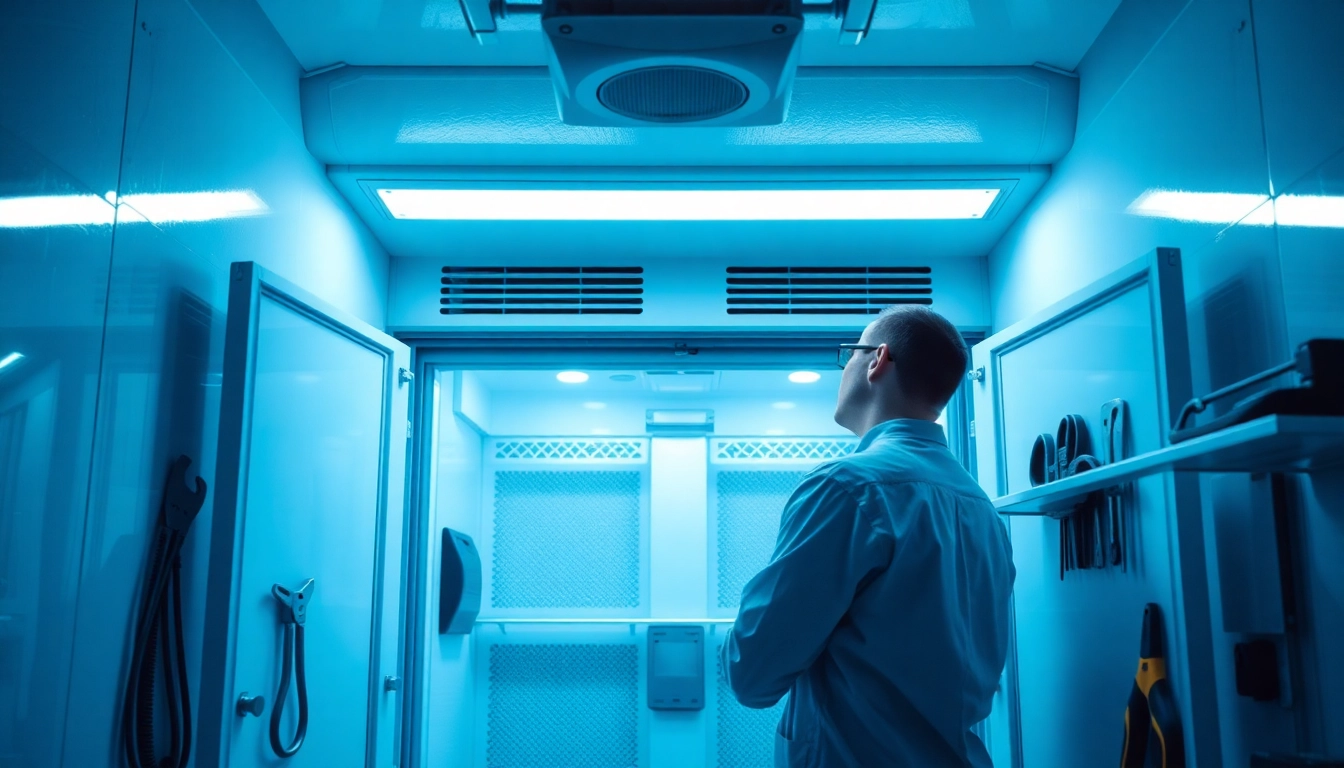
Understanding Walk In Freezer Repair
Walk-in freezers are critical components in various industries, especially in food service and storage sectors. They are designed to maintain low temperatures to safely store perishable goods, ensuring quality and safety. However, like all mechanical systems, they can experience issues that require timely repair. Understanding common problems associated with these units, as well as preventative maintenance, can save businesses time and money. This article offers a comprehensive guide on walk in freezer repair, outlining key components, potential problems, maintenance tips, and choosing a suitable repair service.
What is a Walk In Freezer?
A walk-in freezer is a large refrigerated space that enables businesses to store high volumes of food and other perishable items at low temperatures. Unlike standard freezers, walk-in freezers are designed for heavy-duty use, often featuring a large door for easy access and a floor level that accommodates pallets or shelves stacked high with product. These units can be either self-contained or split systems where the compressor and condenser unit is external to the storage area.
Common Issues Requiring Repair
While walk-in freezers are built for resilience, several common issues may arise, necessitating expert repair services. Here are a few prevalent problems:
- Thermostat Malfunctions: Incorrect temperature settings or malfunctioning thermostats can lead to suboptimal food storage conditions.
- Compressor Failures: The compressor is crucial for maintaining temperature; failure can result from wear and tear or faulty components.
- Frost Build-Up: Excessive frost can block airflow, reducing efficiency and forcing the unit to work harder.
- Leaking Refrigerant: Refrigerant leaks not only reduce efficiency but can also cause environmental hazards.
- Door Seal Issues: Worn or damaged door gaskets can lead to heat infiltration, raising energy costs and compromising stored items.
Signs You Need Professional Repair Services
Recognizing when to call in a professional for repairs can save time and resources. Key indicators include:
- Unusual noises coming from the unit.
- Temperature fluctuations despite thermostat settings.
- Ineffective cooling, where stored items are thawing or not maintaining appropriate temperatures.
- Increased energy bills indicating inefficiency.
- Visible leaks or puddles around the unit.
Key Components of Walk In Freezers
Understanding the main components of walk-in freezers is essential for diagnosing issues and planning repairs effectively. Let’s explore these crucial parts closely.
Compressor Function and Importance
The compressor is often referred to as the heart of the walk-in freezer. Its main function is to compress refrigerant gas, sending it to the condenser. This process is vital for maintaining low temperatures within the unit. Problems with the compressor, such as motor failure or refrigerant leaks, can disrupt cooling efficiency, leading to spoilage of perishable goods.
Evaporator and Condenser Coils
Evaporator coils are located within the freezer and absorb heat from the inside air while releasing cooled air back into the space. Condenser coils, typically located outside the unit, expel the heat absorbed by the refrigerant. Dirty or blocked coils can severely hinder the performance of both systems, leading to increased operational costs and repair needs.
Thermostat and Temperature Control Issues
The thermostat controls the temperature by regulating the compressor’s operation. If the thermostat is miscalibrated or broken, it may fail to signal the compressor to turn on or shut off at the correct times, resulting in inadequate cooling or overcooling. Regular checks and maintenance of the thermostat are crucial for optimal performance.
DIY Maintenance Tips for Walk In Freezers
Preventative maintenance is the best approach to ensuring the longevity and efficacy of walk-in freezers. Engaging in regular upkeep can help identify problems early and reduce the likelihood of requiring emergency repairs.
Regular Cleaning Techniques
Keeping a walk-in freezer clean is essential for performance efficiency. Regularly schedule cleaning of coil fins, evaporator coils, and other areas where dust and debris can accumulate. Use a vacuum or a soft brush to carefully remove any buildup without damaging components.
Monitoring Temperature Logs
Implementing a system for monitoring temperature logs is vital. Many modern walk-ins have digital monitoring systems, but manually checking temperature readings daily should be part of your routine. This process helps catch temperature fluctuations early before they become problematic.
Inspecting Door Seals and Gaskets
Door seals are essential for maintaining temperature and efficiency. Regularly inspect the gaskets for wear and tear. If you notice cracks, separations, or physical damage, they should be replaced promptly to prevent cold air escape and energy waste.
Choosing the Right Repair Service
When it’s time to seek professional help, knowing how to choose the right repair service can make all the difference in ensuring your walk-in freezer is fixed efficiently and reliably. Here are key considerations:
What to Look for in a Service Provider
When vetting potential repair services, consider the following:
- Experience in commercial refrigeration and specific knowledge about walk-in freezers.
- Availability of emergency services, since refrigerator issues can often require immediate attention.
- Positive reviews and testimonials from previous clients.
- Licensing and insurance to protect both parties in case of an accident.
Questions to Ask Before Hiring
Prior to making a hiring decision, ask potential service providers these critical questions:
- What is your response time for urgent repairs?
- Do you provide a warranty for the repairs you perform?
- Can you provide references from previous clients?
- What are your rates for labor and parts?
Importance of Experience and Credentials
Look for service providers with substantial experience dealing with commercial refrigeration systems. Technicians should have relevant certifications that demonstrate their expertise and knowledge of modern walk-in freezer technologies. Providers with industry credentials are more likely to deliver quality service and comply with safety regulations.
Cost Factors in Walk In Freezer Repair
The costs associated with repairing walk-in freezers can vary widely based on several factors. It’s essential to understand these variables to budget appropriately for necessary repairs.
Average Repair Costs and Breakdown
The average cost of repairing a walk-in freezer generally ranges from $150 to $2,000, depending on various elements including:
- Type of repair needed: basic repairs may be cheaper whereas compressor replacements can push costs higher.
- Parts prices: OEM parts may cost more than generic replacements.
- Labor costs: rates can vary based on location and technician expertise.
When to Consider Replacement Instead of Repair
In some cases, replacing your walk-in freezer may be a more prudent choice than repairing it, particularly if repairs become frequent or costly. Consider replacement when:
- The unit is older than 15 years and consistent repairs are necessary.
- Refrigeration efficiency is so low that energy bills are unsustainable.
- Safety and food storage regulations are increasingly difficult to meet due to the freezer’s age or functionality.
Emergency Repair Options and Their Costs
In emergencies, quick repairs are crucial, especially in the food industry. Emergency repair services might cost more due to urgency but can save significant losses. Always inquire about these costs beforehand to be prepared for unexpected expenses.
Conclusion
Walk-in freezers play a vital role in preserving food and other perishable goods for businesses. Understanding their operation, components, and maintenance needs can significantly reduce downtime and repair costs. By recognizing the signs of malfunction, implementing regular maintenance, and choosing reliable service providers, business owners can enhance the operational efficiency of their walk-in freezers while ensuring compliance with health and safety standards. Investing in expert walk in freezer repair services when needed will lead to better performance and longevity, safeguarding valuable assets for years to come.
Leave a Reply