Kuboata: Hochwertige Traktoren für effiziente Landwirtschaft
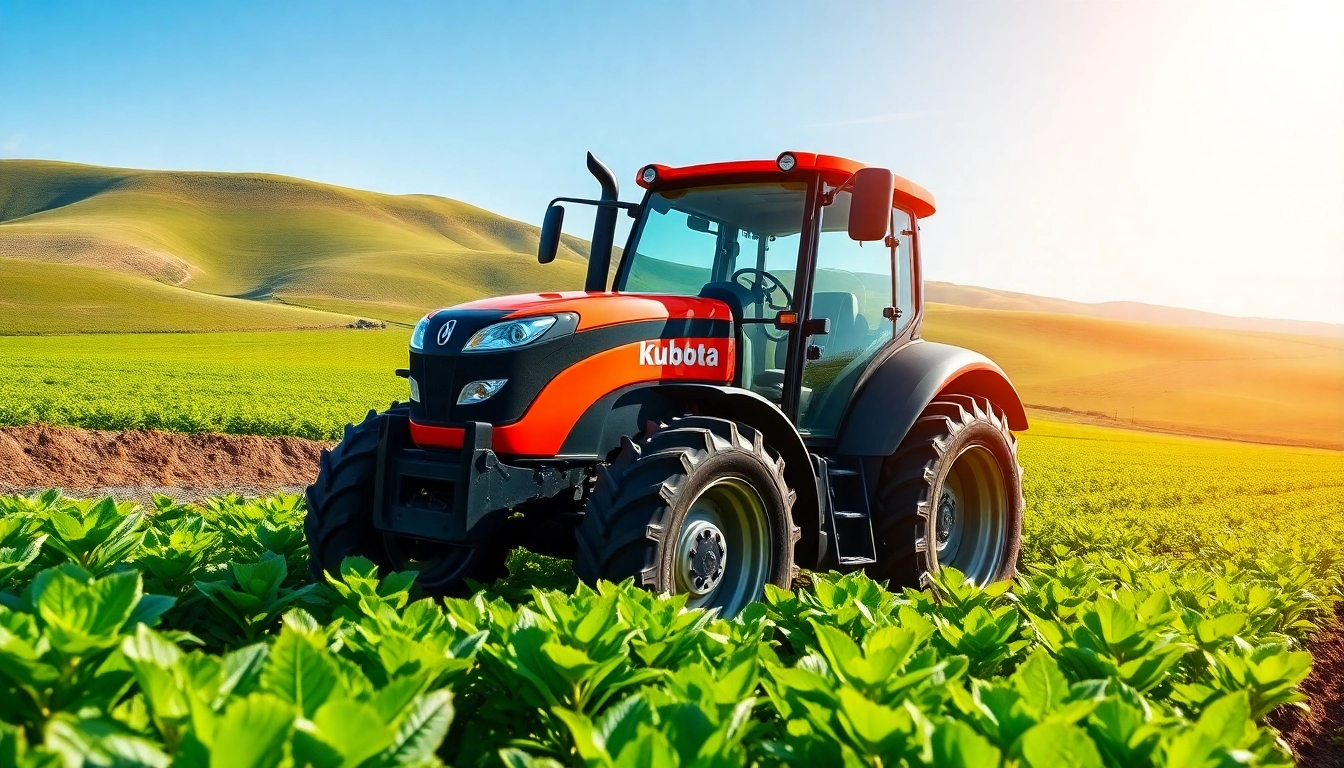
Einführung in Kuboata
Kuboata ist ein Name, der in der aktuellen Agrar- und Bauindustrie zunehmend an Bedeutung gewinnt. Der japanische Hersteller hat sich dafür entschieden, robuste und zuverlässige Maschinen zu entwickeln, die sowohl Landwirten als auch Unternehmen in der Bauwirtschaft zugutekommen. Mit einer Geschichte, die bis ins Jahr 1890 zurückreicht, ist Kuboata nicht nur eine Marke, sondern ein Synonym für Qualität und Innovation. In diesem Artikel werden wir die verschiedenen Aspekte von Kuboata näher beleuchten, von der Geschichte bis zu den neuesten Produktinnovationen. Für eine umfassende Übersicht und Details zu Kuboata finden Sie hier alle relevanten Informationen.
Was ist Kuboata?
Kuboata ist ein multinationales Unternehmen mit Sitz in Osaka, Japan. Es hat sich auf die Entwicklung und den Vertrieb von landwirtschaftlichen Maschinen, Traktoren, Baugeräten und weiteren Maschinen spezialisiert. Die Produktpalette reicht von kleinen Subkompakttraktoren bis hin zu großen landwirtschaftlichen Maschinen, die für verschiedene Anwendungen in der Landwirtschaft und im Bauwesen konzipiert sind. Kuboata steht für Effizienz, Langlebigkeit und technologische Innovation und ist auf dem globalen Markt stark vertreten.
Die Geschichte von Kuboata
Die Gründung von Kuboata datiert auf das Jahr 1890, als die Marke mit der Herstellung von Gießereiprodukten begann. Im Laufe der Jahre entwickelte sich das Unternehmen weiter und diversifizierte seine Produktpalette. In den 1920er Jahren begann Kuboata mit der Herstellung von landwirtschaftlichen Traktoren, was eine entscheidende Wende in der Unternehmensgeschichte darstellt. Seitdem hat Kuboata kontinuierlich in Forschung und Entwicklung investiert, um seine Maschinen zu optimieren und den sich ändernden Anforderungen der Branche gerecht zu werden. Mit einer starken Präsenz in über 110 Ländern hat Kuboata seinen Platz als einer der führenden Hersteller im landwirtschaftlichen Sektor gefestigt.
Die Bedeutung von Kuboata in der Landwirtschaft
Kuboata spielt eine entscheidende Rolle in der modernen Landwirtschaft. Die Produkte des Unternehmens helfen Landwirten, ihre Effizienz zu steigern und die Produktivität zu maximieren. Die Traktoren von Kuboata sind für ihre Zuverlässigkeit und Leistungsfähigkeit bekannt, was sie zu einer bevorzugten Wahl für viele Landwirte macht. Insbesondere in Zeiten von klimatischen Veränderungen und wachsendem Druck auf die landwirtschaftliche Produktion ist Kuboata in der Lage, innovative Lösungen anzubieten, die den Landwirtschaftsbetrieben helfen, nachhaltig und effizient zu arbeiten. Diese Bedeutung zeigt sich nicht nur in der Qualität der Produkte, sondern auch in der tieferen Verpflichtung des Unternehmens zur Förderung umweltfreundlicher Praktiken in der Landwirtschaft.
Produkte von Kuboata
Traktoren für verschiedene Anwendungen
Kuboata bietet eine breite Palette von Traktoren an, die für verschiedene Anwendungen in der Landwirtschaft und im Bauwesen ausgelegt sind. Dazu gehören:
- Subkompakttraktoren: Ideal für kleinere Flächen und leichte Aufgaben im Gartenbau.
- Komforttraktoren: Diese Traktoren sind für mittelgroße Betriebe konzipiert und bieten eine ausgezeichnete Kombination aus Leistung und Ergonomie.
- Variabler Traktoren: Ausgelegt für große landwirtschaftliche Betriebe, die intensive Arbeiten durchführen müssen.
- Mini-Bagger und Lader: Diese Maschinen sind für Bauarbeiten und Landschaftsbau konzipiert und bieten vielseitige Einsatzmöglichkeiten.
Die Traktoren von Kuboata sind mit modernen Technologien ausgestattet, die eine einfache Bedienung und Wartung ermöglichen. Beispielsweise verfügen viele Modelle über fortschrittliche Diagnose-Systeme, die es dem Bediener ermöglichen, den Gerätezustand in Echtzeit zu überwachen und entsprechend zu handeln.
Landmaschinen und Zubehör
Kuboata produziert nicht nur Traktoren, sondern auch eine Vielzahl von Landmaschinen und Zubehörteilen, die den Landwirten helfen, ihre Aufgaben noch effizienter zu erledigen. Dazu gehören:
- Plattformen und Anhänger: Für den Transport von Erzeugnissen und Material auf dem Feld.
- Düngerstreuer und Pflanzmaschinen: Für die gezielte Ausbringung von Dünger und die präzise Saat.
- Bodenbearbeitungsgeräte: Diese Geräte helfen dabei, den Boden für die Aussaat vorzubereiten, indem sie ihn auflockern und aufbereiten.
Kuboata legt großen Wert auf die Qualität der verwendeten Materialien bei der Herstellung dieser Maschinen. Dies stellt sicher, dass die Produkte langlebig sind und auch unter harten Bedingungen zuverlässig funktionieren.
Technologische Innovationen bei Kuboata
Innovation ist ein zentraler Bestandteil der Unternehmensphilosophie von Kuboata. Das Unternehmen investiert erheblich in Forschung und Entwicklung, um neue Technologien zu erforschen, die die Effizienz ihrer Maschinen und die Benutzerfreundlichkeit verbessern. Einige bemerkenswerte Innovationen sind:
- Automatisierungssysteme: Diese Systeme ermöglichen eine Teilautomatisierung unserer Traktoren, was zu einer höheren Genauigkeit und weniger Bedienfehlern führt.
- Umweltfreundliche Technologien: Kuboata arbeitet an Maschinen, die weniger Emissionen produzieren und effizienter mit Ressourcen umgehen.
- Smart Farming Lösungen: Innovative Software und Sensoren, die Landwirten helfen, ihre Betriebsabläufe besser zu überwachen und zu steuern.
Diese Technologien tragen nicht nur zur Verbesserung der Produktivität bei, sondern fördern auch nachhaltige Praktiken in der Anbauweise, was in der heutigen Zeit von großer Bedeutung ist.
Kuboata im Vergleich zu Konkurrenten
Kuboata versus andere Marken
Im Vergleich zu anderen Marken hat Kuboata einige Vorteile, die es hervorheben. Obwohl andere Hersteller in der Branche ebenfalls hochwertige Maschinen herstellen, bietet Kuboata eine umfassendere Palette an Traktoren, die für unterschiedlichste Anwendungen optimiert sind. Zum Beispiel hat Kuboata in einem großen Marktsegment den Vorteil des guten Preis-Leistungs-Verhältnisses, ohne dabei Kompromisse bei der Qualität einzugehen. Einige Wettbewerber konzentrieren sich hauptsächlich auf spezialisierte Maschinen, während Kuboata von kleinen anwenderfreundlichen Traktoren bis hin zu schweren Maschinen alles anbietet.
Kundenbewertungen und Erfahrungen
Die Bewertungen und Erfahrungen von Kunden sind ein entscheidender Indikator für die Leistung und Zuverlässigkeit der Produkte. Viele Landwirte und Bauunternehmer berichten von ihrer Zufriedenheit mit den Maschinen von Kuboata. Die häufigsten Lobeshymnen beziehen sich auf die Benutzerfreundlichkeit, die robuste Bauweise und die hohe Leistung unter realen Arbeitsbedingungen. Ein weiterer positiver Aspekt, der oft erwähnt wird, ist der Kundenservice; Kuboata lässt seinen Kunden in Wartungsfragen nicht allein und bietet umfassende Unterstützung durch sein Händlernetzwerk.
Marktanalyse und Trends
Die Agrar- und Baumaschinenbranche durchlebt derzeit einen Wandel, insbesondere mit dem Aufkommen neuer Technologien und dem wachsenden Interesse an nachhaltigen Praktiken. Unternehmen wie Kuboata müssen sich diesen Trends anpassen, um relevant zu bleiben. Datenanalysen zeigt, dass der Bedarf an präzisen Maschinen, die Daten in der Landwirtschaft nutzen, weiter zunehmen wird. Das Unternehmen hat bereits reagiert, indem es Produkte anbietet, die mit Smart Farming-Technologien ausgestattet sind, um den Landwirten zu helfen, ihre Erträge zu maximieren.
Kauf von Kuboata-Produkten
Wo Kuboata-Produkte kaufen
Kuboata-Produkte sind in einer Vielzahl von Verkaufsstellen erhältlich, darunter autorisierte Händler, Online-Shops und auf Agrarmessen. Die Suche nach einem geeigneten Händler kann über die offizielle Kuboata-Webseite erfolgen, wo die nächstgelegenen Verkaufsstellen sowie spezifische Informationen zu den verfügbaren Produkten bereitgestellt werden. Aufgrund der breiten Angebotspalette ist es für Käufer wichtig, einen Händler zu finden, der das gewünschte Produkt und die dazugehörigen Dienstleistungen anbieten kann.
Finanzierungsoptionen bei Kuboata
Um den Erwerb von Kuboata-Produkten für Landwirte und Unternehmen zu erleichtern, bietet Kuboata verschiedene Finanzierungsoptionen an. Diese reichen von günstigen Ratenfinanzierungen bis hin zu Leasing-Modellen, die es den Käufern erlauben, die Maschinen ohne große Anfangsinvestitionen zu nutzen. Außerdem stehen oft spezielle Angebote und Rabatte zur Verfügung, die den Kauf weiter fördern. Käufer sollten sich über alle verfügbaren Optionen informieren, um die für sie passende Lösung zu finden.
Wartung und Service
Eine ordnungsgemäße Wartung ist entscheidend für die lange Lebensdauer und Leistung jeder Kuboata-Maschine. Der Hersteller bietet regelmäßige Wartungsprogramme und Schulungen an, um sicherzustellen, dass die Kunden die besten Praktiken für die Instandhaltung ihrer Geräte kennen. Viele Händler bieten auch schnellen und effektiven Reparaturservice an, um Ausfallzeiten zu minimieren und die Effizienz der Maschinen zu maximieren. Zudem sind originale Ersatzteile leicht verfügbar, was die Wartung erleichtert.
Zukunftsaussichten für Kuboata
Erweiterungspläne und neue Produkte
Die Zukunft von Kuboata sieht vielversprechend aus, da das Unternehmen kontinuierlich plant, sein Produktportfolio zu erweitern. Es wurden bereits neue Modelle angekündigt, die auf aktuelle Marktbedürfnisse reagieren – insbesondere in der Automatisierung und Digitalisierung. Auch die Entwicklung umweltfreundlicher Maschinen wird weiter vorangetrieben, um die steigenden Anforderungen an Nachhaltigkeit zu erfüllen, die in der Branche zunehmend gefordert werden.
Nachhaltigkeit und umweltfreundliche Praktiken
Kuboata setzt auf nachhaltige Praktiken und Technologien, die nicht nur die Effizienz der Maschinen verbessern, sondern auch die Umwelt schonen. Die Entwicklung von Maschinen mit niedrigen Emissionen und hohem Treibstoffverbrauch ist ein Beispiel dafür, wie das Unternehmen umweltbewusste Entscheidungen trifft. Diese Strategie wird durch Partnerschaften mit verschiedenen Umweltschutzorganisationen ergänzt, um den Übergang zu nachhaltigeren landwirtschaftlichen Praktiken zu unterstützen.
Marktentwicklungen und Innovationen
Mit der wachsenden Bedeutung von Technologie in der Landwirtschaft ist Kuboata gut positioniert, um von diesen Marktentwicklungen zu profitieren. Der Fokus liegt auf der Integration von IoT (Internet der Dinge) in die Maschinen, was Landwirten helfen kann, den Betriebsablauf zu optimieren. Die neuen Produkte, die Kuboata einführt, zielen darauf ab, eine umfassende Lösung zu bieten, die nicht nur die Maschinen selbst, sondern auch die gesamte Betriebsführung umfasst.