Choosing the Right Hydrogen Gas Detector for Your Safety Needs
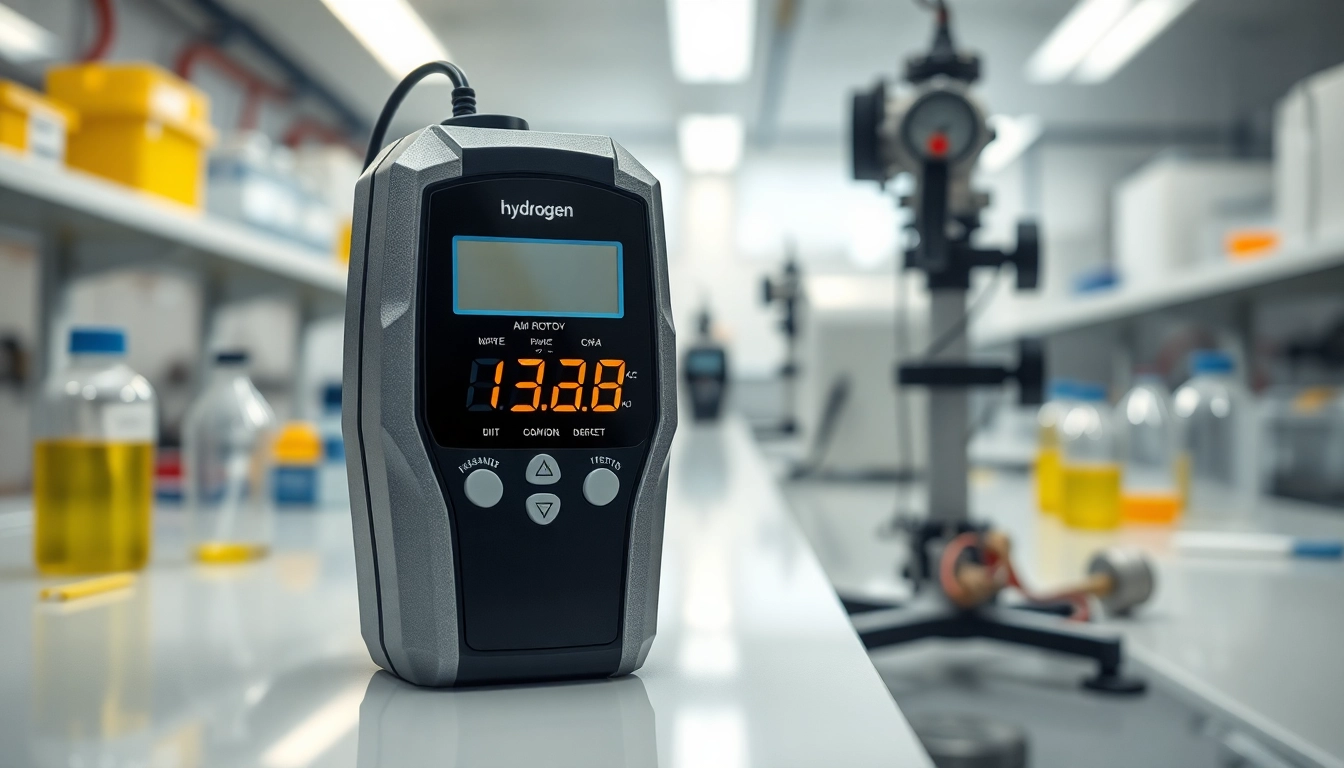
Understanding Hydrogen Gas Detectors
What Is a Hydrogen Gas Detector?
A hydrogen gas detector is a critical safety device designed to detect the presence of hydrogen gas in the environment. Hydrogen, while useful in various industrial applications, is highly flammable and poses significant risks in terms of explosion and fire hazards. These detectors serve as an early warning system, enabling businesses and individuals to take appropriate action when hydrogen levels become dangerous. The significance of hydrogen gas detectors cannot be overstated, particularly in sectors such as petrochemical, manufacturing, and laboratory environments where hydrogen is commonly used or produced.
By integrating state-of-the-art technology, such as the Hydrogen gas detector, industries can enhance their safety protocols and protect both personnel and property from potential hazards associated with hydrogen leaks.
How Hydrogen Gas Detectors Work
Hydrogen gas detectors utilize various technologies to sense the presence of hydrogen in the air. The most common types include electrochemical sensors, infrared sensors, and catalytic sensors. Each of these technologies has its unique principles of operation.
- Electrochemical Sensors: These sensors detect hydrogen gas through a chemical reaction that generates an electrical signal. When hydrogen molecules enter the sensor, they undergo oxidation at the anode, producing a flow of current that correlates directly with the concentration of hydrogen present.
- Infrared Sensors: These devices use infrared light to detect hydrogen. When hydrogen gas is present, it absorbs specific wavelengths of infrared light, altering the intensity of the light reaching the sensor. This change is then translated into gas concentration levels.
- Catalytic Sensors: These sensors work by employing oxidation reactions at a catalytic surface. When hydrogen gas is present, it reacts with the catalyst, resulting in a temperature increase that is proportional to the gas concentration.
Common Applications for Hydrogen Gas Detectors
Hydrogen gas detectors find applications across various sectors due to the versatility and prevalence of hydrogen as a fuel and chemical feedstock. Some of the common applications include:
- Petrochemical Industries: In facilities that process or utilize hydrogen for refining operations, detecting hydrogen leaks is critical to prevent explosive atmospheres.
- Hydrogen Production Facilities: As more companies invest in renewable hydrogen production, the need for reliable detection systems becomes paramount.
- Electronics Manufacturing: The semiconductor industry often employs hydrogen in various processes, making detection a necessary safety measure.
- Laboratories: Research and development environments that involve hydrogen also mandate the use of gas detectors to ensure a safe working atmosphere.
Types of Hydrogen Gas Detectors
Electrochemical vs. Infrared Detectors
When selecting a hydrogen gas detector, it’s essential to understand the differences between electrochemical and infrared detectors, as each type has its advantages and suitable use cases.
- Electrochemical Detectors: These detectors are highly sensitive and can detect very low concentrations of hydrogen, making them ideal for environments where safety is paramount. They tend to be cost-effective but may require periodic calibration and replacement of sensor components.
- Infrared Detectors: Infrared detectors excel in detecting higher concentrations of hydrogen and are less prone to poisoning by other chemicals. However, they are typically more expensive and require specific environmental conditions for optimal functionality.
Choosing the Right Type for Your Needs
Choosing the appropriate hydrogen gas detector hinges on several factors: the specific application, the environment in which the detector will be used, and the sensitivity required. Here are some considerations to take into account:
- Application Type: Consider the industry and specific processes where hydrogen is used. Industrial settings may need robust and highly sensitive detectors, whereas smaller laboratories may opt for simpler systems.
- Environmental Conditions: Factors such as temperature, humidity, and the presence of other gases can impact sensor performance. Select a detector that is suited to the environmental conditions of your facility.
- Response Time: The speed at which a detector can identify the presence of hydrogen is vital in emergency situations. Choose a system that has quick response times to ensure safety.
Key Features to Look For
When evaluating various hydrogen gas detectors, look for key features that enhance performance and safety:
- Real-Time Monitoring: Continuous monitoring capabilities provide instant alerts, allowing for timely action if hydrogen is detected.
- Calibration Alerts: Detectors that remind users when calibration is needed can help maintain accuracy over time.
- Data Logging and Reporting: Detectors that can log and store data facilitate compliance with safety regulations and allow for trend analysis over time.
- Portability: For applications requiring mobility, lightweight and battery-operated models are advantageous.
Installation and Maintenance
Steps for Proper Installation
Installing a hydrogen gas detector requires careful planning and adherence to best practices to ensure optimal performance:
- Site Assessment: Conduct a thorough assessment of the area where the detector will be installed, identifying potential leak sources and high-traffic areas.
- Select the Location: Install the detector in a location where hydrogen is likely to accumulate, typically near potential leak sources, but not in direct contact with probable water ingress or steam.
- Mounting: Follow manufacturer instructions for mounting the device securely, ensuring that it is at the appropriate height for effective gas detection.
- Power Supply: Ensure a stable power supply, utilizing backup systems if necessary to maintain operation during power outages.
- Initial Calibration: Perform initial calibration as per manufacturer guidelines to ensure accuracy from the start.
Routine Maintenance Practices
Consistency in maintenance is vital to ensure ongoing reliability and accuracy of hydrogen gas detectors:
- Regular Calibration: Depending on the manufacturer’s guidelines, routine calibration should be performed to ensure the detector operates within specified accuracy levels.
- Visual Inspections: Regularly inspect the detector for any physical damage, corrosion, or other issues that may impair functionality.
- Replacement of Sensors: Pay attention to the recommended lifespan of sensors and be proactive in replacing them to maintain detection capabilities.
- Functional Testing: Conduct functional tests to ensure that the detector is responsive when presented with a known concentration of hydrogen.
Troubleshooting Common Issues
Despite rigorous maintenance, issues may still arise with hydrogen gas detectors. Here are some common problems and recommended solutions:
- No Alarm Triggered: Inspect the calibration and check the power supply. If improperly calibrated or switched off, the detector may not function as expected.
- False Alarms: Such alarms may arise from environmental factors or sensor contamination. Conduct a cleaning and recalibration routine to mitigate false alarms.
- Sensitivity Issues: If sensitivity appears diminished, check sensor integrity and consider replacement if necessary.
Safety Standards and Regulations
OSHA and Other Regulatory Bodies
Ensuring compliance with safety standards is essential to mitigate risks associated with hydrogen gas. The Occupational Safety and Health Administration (OSHA) sets fundamental safety regulations that govern hydrogen gas detection. Other bodies, such as the National Fire Protection Association (NFPA) and the American National Standards Institute (ANSI), provide guidelines that further detail specific requirements for gas detection systems.
Compliance Requirements for Businesses
Businesses utilizing hydrogen must adhere to specific compliance standards to avoid penalties and ensure worker safety. Key requirements include:
- Gas Detection Systems: Installing hydrogen gas detectors in applicable areas is often mandated to ensure employee safety.
- Training Programs: Companies must implement training for staff on the proper use of gas detectors and actions to take in the event of gas detection.
- Record Keeping: Maintaining records of inspections, maintenance, and employee training related to hydrogen safety is critical for audits and compliance verification.
Best Practices for Safe Use
Implementing best practices for the use of hydrogen gas detectors can significantly enhance safety:
- Employee Training: Regularly train employees to understand the functionality of detectors and the relevant protocols in case of alarm activation.
- Emergency Procedures: Establish clear emergency procedures that outline the steps to be taken based on detector readings.
- Regular Drills: Conduct safety drills to ensure preparedness for potential hydrogen leaks, reinforcing learned protocols.
Future Trends in Gas Detection Technology
Innovative Features on the Horizon
The field of gas detection, including hydrogen gas detection, is continually evolving. Future advancements may introduce features such as enhanced sensor capabilities, smaller and more portable detectors, and automation of maintenance requirements, enhancing overall user experiences and safety.
The Role of IoT in Gas Detection
The Internet of Things (IoT) is poised to reshape gas detection technologies. With IoT-enabled detectors, real-time data analysis and remote monitoring become more attainable. These connected systems can send alerts to smartphones or control panels when gas is detected, enabling quicker responses and more efficient management of gas safety protocols.
Preparing for Future Safety Challenges
As industries continue to integrate hydrogen into processes, emerging technologies will address potential new safety challenges. Businesses need to stay informed about technological advancements as well as regulatory updates, adjusting their safety strategies accordingly to create robust systems that ensure employee safety and environmental protection.