Enhancing Pipeline Integrity: Key Considerations for Pipe Stress Company Analysis
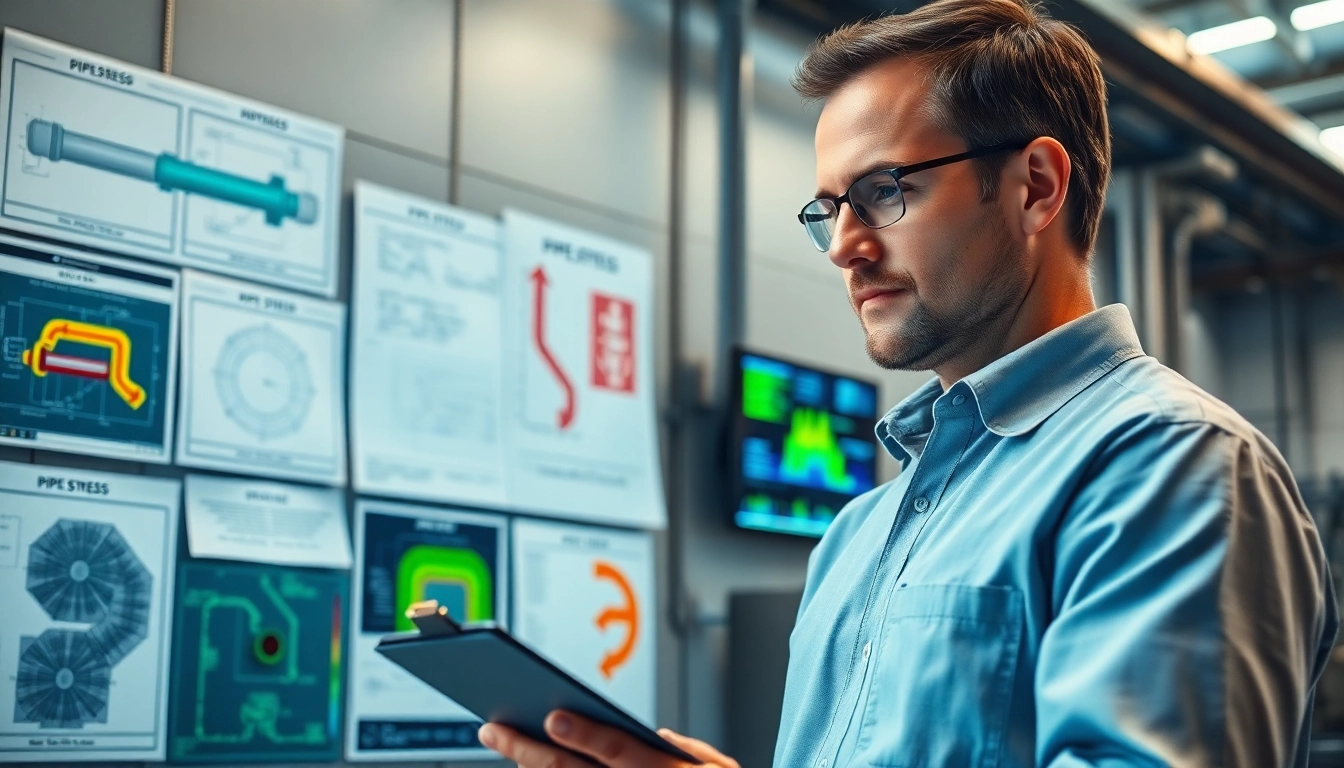
Understanding Pipe Stress Analysis
What is Pipe Stress Analysis?
Pipe stress analysis refers to the evaluation of the mechanical integrity of piping systems under varying conditions of load, temperature, and pressure. This analysis is critical in ensuring that piping systems operate safely and efficiently without experiencing material degradation or failure. In essence, it involves assessing the stress and strain states within pipes and their supporting structures, determining how these elements respond to internal and external pressures.
The primary goal of pipe stress Company analysis is to predict potential failures caused by thermal expansion, weight, fluid dynamics, and environmental factors. Professionals in this field employ sophisticated techniques, including Finite Element Analysis (FEA) and advanced software tools, to model pipe behavior under different scenarios, establishing guidelines for design and installation.
Importance of Pipe Stress for Safety
Understanding pipe stress is paramount for maintaining safety across various industries, including oil and gas, chemical processing, and water treatment. High stress levels can lead to catastrophic failures such as leaks, ruptures, or thermal buckling, posing threats not only to infrastructure but also to human lives and the environment. Therefore, regular pipe stress analysis ensures compliance with safety regulations and industry standards, helping to prevent accidents and maintain the reliability of operations.
Moreover, effective pipe stress management contributes to longevity and durability. By identifying stress points early in the design phase or during inspections, companies can implement recommended solutions, such as adjusting supports or utilizing expansion joints, greatly mitigating risks.
The Role of a Pipe Stress Company in Projects
A dedicated pipe stress company provides specialized expertise during every phase of project development—designing, planning, and executing piping systems. These companies have the technical knowledge and tools necessary for comprehensive stress analysis, ensuring that all piping systems endure operational demands. Their role includes collaborating with engineers and project managers to optimize designs, predict the behavior of piping systems, and recommend the most effective materials and installation techniques.
Additionally, pipe stress companies are integral during project commissioning, providing requisite documentation that confirms compliance with safety and quality standards. This thorough approach not only helps in project validation but also aids in future maintenance planning.
Common Challenges Faced by Pipe Stress Companies
Identifying Stress Points in Pipeline Systems
One of the most significant challenges in pipe stress analysis is accurately identifying stress points across complex piping networks. Due to the interaction of various forces, including thermal expansion, gravitational loads, and dynamic forces from fluid movement, engineers must analyze each segment of the pipeline in detail. This is particularly challenging in large facilities with intricate layouts, where minor changes can create unforeseen stress concentrations.
Furthermore, inconsistent material properties and poor installation practices can lead to unexpected stress points. Thus, comprehensive pre-analysis inspections are necessary to gather baseline data, which informs subsequent modeling efforts. In many cases, the use of real-time monitoring technology can enhance stress point identification, allowing for proactive interventions.
Software and Tools for Accurate Analysis
The technological landscape for pipe stress analysis is continually evolving, with numerous specialized software packages available that aid engineers in performing detailed evaluations. Programs like CAESAR II, AutoPIPE, and ANSYS are widely used for simulating pipe behavior under various loading scenarios. These tools provide detailed graphical representations and calculation outputs that facilitate an easier understanding of stress distributions throughout the piping system.
While these software solutions are instrumental, the accuracy of their results heavily relies on the quality of input data. Engineers must ensure that parameters such as material properties, temperature variations, and load conditions are meticulously specified. Moreover, continuous training and proficiency development in these software platforms remain essential to maximize their effectiveness in risk assessment and management.
Compliance with Industry Regulations
Adherence to industry standards and regulations complicates pipe stress analysis but is non-negotiable for safety and environmental protection. There are various regulations, such as ASME B31 for piping, API specifications for the oil and gas industry, and other local regulations, that dictate how stress analysis must be conducted.
Navigating these regulations requires a deep understanding of the specific requirements, calculations, and documentation needed for various projects. Regular updates and revisions to these standardsmean that professionals must be aware of the latest changes and how they impact current and future projects. Compliance not only ensures legal and operational integrity but also enhances the reputation of the employing organization.
Best Practices for Pipe Stress Management
Regular Maintenance and Inspections
Consistent maintenance and inspection regimes are vital for ensuring the integrity of piping systems over time. Regular checks for wear and tear, potential corrosion, and material fatigue help identify problem areas before they evolve into severe issues. Implementing a scheduled maintenance program, complete with detailed documentation, ensures that all stakeholders can monitor the system’s condition accurately.
Additionally, employing technology like non-destructive testing (NDT) can assist in evaluating the health of pipes without causing further damage. Timely inspections, when coupled with proactive repair or replacement strategies, can significantly extend the operational life of pipelines in various environments.
Using Advanced Modeling Techniques
Utilizing advanced modeling techniques in pipe stress analysis, such as 3D modeling and FEA, allows engineers to evaluate systems more comprehensively. These methods provide a more realistic visualization of how the piping system will respond to various conditions over time. Modeling enables engineers to consider factors that may not be immediately apparent, such as interactions between different components and the effects of environmental conditions.
Furthermore, the increase in computational power has facilitated increasingly sophisticated modeling, enabling simulations that were previously unimaginable. This evolution empowers engineers to perform what-if scenarios, optimizing designs even further and ensuring that every contingency is accounted for.
Training and Certification for Engineers
The complexity of pipe stress analysis necessitates that engineers possess both theoretical knowledge and practical skills. Therefore, ongoing training and certification in the latest techniques, software, and industry standards are essential for professionals in this domain. Organizations can bolster their approach by creating programs that encourage continuous education and skill development, fostering a culture of learning within the company.
Certification from recognized bodies like the American Society of Mechanical Engineers (ASME) can enhance an engineer’s credentials and increase the overall competency level of teams. Additionally, investment in professional development not only increases employee satisfaction but also reinforces the credibility of the organization within the market.
Case Studies of Successful Pipe Stress Applications
Transportation Sector Innovations
Pipe stress analysis has been instrumental in the development of innovative solutions across the transportation sector. For instance, in the renovation of a major urban airport, a comprehensive pipeline rerouting project required detailed stress analysis to ensure efficient fluid transport without compromising structural integrity. Through meticulous stress calculations, the design team was able to utilize lightweight materials and minimize the support structures required, resulting in significant cost savings and enhanced operational efficiency.
This project exemplified how thoughtful pipe stress analysis could lead to innovative practices, not only improving safety but also fostering sustainability through reduced material waste.
Energy Industry Adjustments
The energy industry frequently encounters rigorous pipe stress challenges, especially during the construction of pipelines for oil and gas transport. A notable case involved an offshore pipeline project where engineers encountered extreme environmental conditions including substantial wave forces and thermal expansion. An in-depth pipe stress analysis helped to determine the optimal pipe sizes and materials to withstand these stresses, significantly reducing the risk of pipeline failure and environmental disasters.
The project took advantage of recent software advances, employing dynamic simulations to model the behavior of the pipeline under various conditions, thus reinforcing its structural resilience.
Sustainable Practices in Pipe Stress Analysis
The integration of sustainable practices in pipe stress analysis is becoming increasingly crucial as industries strive to minimize their environmental footprint. For instance, using recycled materials for piping systems not only contributes to environmental sustainability but requires careful consideration during the stress analysis phase to account for differences in material properties and performance compared to traditional materials.
By adapting stress analysis practices to include sustainability as a core component, companies can enhance their overall project efficiencies and align their operations with global green initiatives. This approach benefits both the planet and the organization’s bottom line.
Future Trends in Pipe Stress Analysis
Emerging Technologies Impacting the Industry
The future of pipe stress analysis is poised to be revolutionized by emerging technologies such as Artificial Intelligence (AI) and machine learning, which promise to enhance predictive analytics in pipeline systems. These technologies enable the processing of vast amounts of data to predict stress failures before they occur, facilitating a more proactive approach to pipeline management.
Additionally, the continued development of sensor technology and the Internet of Things (IoT) will allow for real-time monitoring of pipe conditions, giving operators the ability to respond instantaneously to any potential issues. As these technologies become more affordable and accessible, they will undoubtedly reshape how pipe stress analysis is conducted and managed.
Regulations and Standards Evolution
The landscape of regulations governing pipe stress analysis is constantly evolving, with organizations like the American National Standards Institute (ANSI) and the International Organization for Standardization (ISO) working towards stricter compliance protocols. This dynamic environment creates both challenges and opportunities for professionals in the field, necessitating continuous adaptation to new guidelines and performance metrics.
As regulatory bodies place higher importance on safety and sustainability, adherence will increasingly require innovative solutions and proactive measures. Thus, staying ahead of regulatory trends will become an essential component of successful pipe stress management.
Predictions for the Next Decade in Pipe Stress Management
Looking ahead, advancements in computational capabilities and real-time analytics are set to redefine the future of pipe stress management over the next decade. Predictions include enhanced integration of AI-driven tools that provide iterative learning from past analyses, allowing for continuous improvements in stress prediction accuracy.
Moreover, as industries move towards more sustainable practices, the focus will likely shift towards designing systems that are not only resilient and safe but also environmentally friendly. This holistic approach will reaffirm the importance of pipe stress analysis in sectors that are critical to economic stability and environmental stewardship.
Leave a Reply