Top Liquid Packaging Machine Supplier for Efficient and Reliable Solutions
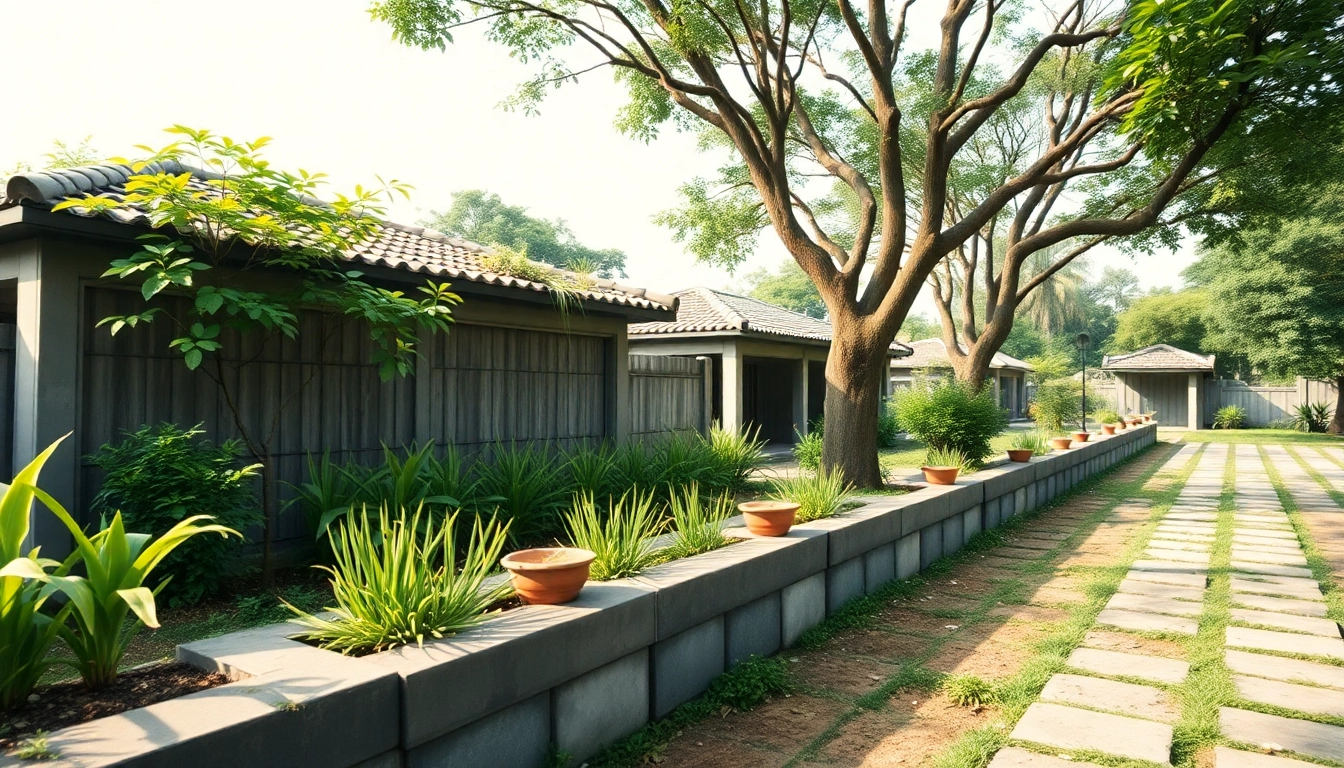
Introduction to Liquid Packaging Machines
What is a Liquid Packaging Machine?
Liquid packaging machines are specialized equipment designed to fill, seal, and package liquid products in various containers. These machines play a vital role in industries such as food and beverage, pharmaceuticals, and chemicals, ensuring that products are delivered to consumers safely and efficiently. Whether it’s a bottle of juice, a jar of sauce, or a vial of medication, liquid packaging machines help maintain product quality while enhancing shelf life and ensuring compliance with safety standards.
History and Development of Packaging Machines
The evolution of liquid packaging machines can be traced back to the early 20th century when manual packaging methods were prevalent. As consumer demand grew and industries sought efficiency, the need for automation led to the development of various filling and sealing machines. In the past few decades, innovations such as inline filling, volumetric filling, and automatic labeling have transformed the packaging landscape. Today, modern machines are characterized by enhanced speed, precision, and adaptability, catering to diverse product types and packaging formats.
Benefits of Choosing a Reliable Supplier
Choosing a trustworthy Liquid Packaging Machine Supplier is crucial for businesses looking to scale. A reliable supplier ensures the provision of high-quality, durable machines that comply with industry standards. Additionally, they can provide after-sales support, including maintenance, technical assistance, and access to spare parts. Building a solid relationship with a supplier also opens doors to innovation and collaboration on customized packaging solutions tailored to specific needs.
Different Types of Liquid Packaging Machines
Automatic Filling Machines
Automatic filling machines are designed for high-speed production environments where precision and efficiency are paramount. These machines operate continuously, reducing the need for manual labor while increasing throughput. They can fill various container sizes and types, from small vials to large drums, making them versatile for different industries. Modern automatic fillers often utilize sensors and advanced software to ensure accuracy and enhance the packaging process, significantly minimizing waste and errors.
Semi-Automatic Filling Machines
Semi-automatic filling machines provide a balanced approach for businesses that may not require the high output of fully automatic machines but still want improved efficiency over manual processes. These machines typically require some operator involvement, such as placing containers or managing the filling process, but can dramatically reduce labor costs and time compared to traditional methods. By investing in semi-automatic machines, businesses can achieve a significant boost in productivity while maintaining flexibility in their operations.
Packaging Machines for Various Food and Beverage Products
The food and beverage industry utilizes a wide range of liquid packaging machines tailored to specific product characteristics. These machines handle everything from water and juices to sauces and creams, accommodating variations in viscosity and particle content. For example, a machine designed for viscous materials will have features such as adjustable speed settings and specialized filling nozzles to ensure consistent results. As consumer preferences evolve, so does the need for innovative packaging solutions that align with trends in sustainability and convenience.
Factors to Consider When Choosing a Supplier
Quality and Reliability of Machines
Quality should be the foremost consideration when selecting a liquid packaging machine supplier. High-quality machines are typically constructed from durable materials that can withstand the rigors of production while maintaining performance. Reliability is also crucial; machines need to operate efficiently with minimal downtime to ensure maximum productivity. Hence, it is advisable to research potential suppliers’ reputations, look for customer testimonials, and analyze their warranties and support services as indicators of quality.
Customer Support and Maintenance
Effective customer support can greatly enhance a company’s operational efficiency. Suppliers offering comprehensive maintenance services can help prevent unexpected downtimes, which can lead to lost revenue. When choosing a supplier, it is important to assess the extent of their support, including training for operators, availability of spare parts, and response times in case of machine failures. A proactive approach to maintenance can extend the lifespan of packaging machines and ensure continued production efficiency.
Innovation in Packaging Technology
The packaging industry is continuously evolving, driven by technological advancements and changing consumer preferences. Suppliers that invest in the latest innovations—such as smart filling systems that integrate with production monitoring software, eco-friendly packaging technologies, and automated cleaning systems—can provide businesses with a competitive edge. It is crucial to partner with a supplier who keeps abreast of trends and invests in research and development to offer cutting-edge solutions to their clients.
Case Studies: Client Success Stories
Analysis of Successful Projects
Examining successful implementations of liquid packaging machines can provide invaluable insights. For example, a mid-sized beverage company faced challenges with filling efficiency and product consistency. After collaborating with a reputable liquid packaging machine supplier, they upgraded to an automatic filler that reduced their filling time by over 35% while enhancing accuracy. This project not only improved production but also resulted in higher customer satisfaction due to improved product quality.
Testimonials from Clients
Client feedback typically offers a candid view of a supplier’s capabilities. One client noted, “After switching to [Supplier X], our production speed increased substantially. The support team is always available, ensuring that we can focus on growing our business.” Such testimonials underscore the importance of partnering with suppliers who prioritize customer relations and support.
Lessons Learned from Implementations
Every project offers learning opportunities. One of the key lessons from various implementations is the importance of thorough planning and requirement analysis. Businesses need to fully understand their production needs and challenges before selecting a machine. Additionally, fostering collaboration between suppliers and clients throughout the installation process leads to successful outcomes as it allows for adjustments based on real-time feedback.
The Future of Liquid Packaging Machines
Current Trends in the Packaging Industry
Several trends are shaping the current landscape of liquid packaging. Sustainability is at the forefront, with many companies looking to reduce plastic usage and explore biodegradable materials. Another trend is the demand for smarter packaging solutions that utilize technology to enhance monitoring and tracking of products throughout the supply chain. As e-commerce continues to expand, the adaptation of packaging techniques that cater to online sales is also gaining traction.
The Role of AI and Automation
Artificial intelligence (AI) and automation are transforming the way packaging machines operate. AI can provide predictive maintenance support, allowing businesses to identify potential issues before they escalate. Automation enhances operational efficiency, reducing the need for manual intervention. As these technologies become more affordable and accessible, businesses that adopt them will likely see increased productivity and better resource management.
Opportunities for Future Innovation
The packaging industry presents numerous opportunities for innovation, particularly in sustainable practices and advanced technologies. Future developments might include machines that can seamlessly switch between different packaging formats or those designed to accommodate packaging customization as consumer preferences become more varied. Additionally, integrating renewable energy sources into packaging processes can significantly reduce environmental footprints, creating a paradigm shift toward more sustainable production.
Leave a Reply